在数控加工的世界里,主轴究竟有多重要?它是否只是实现旋转的一个轴心,还是关系到整台设备运转效率与加工质量的“命脉”?尤其在车削作业中,数控车床主轴的性能直接决定了工件的尺寸精度、表面光洁度以及加工节拍。理解数控车床主轴,不只是看参数,而是要看它如何贯穿整个工艺流程,影响每一道加工细节。
接下来,我们从“核心驱动”、“性能参数”、“主轴类型”、“匹配工艺”、“智能化趋势”、“选型策略”与“日常管理”七个角度,全面拆解数控车床主轴的技术与应用逻辑,带你系统了解这个决定“好加工”的关键部件。
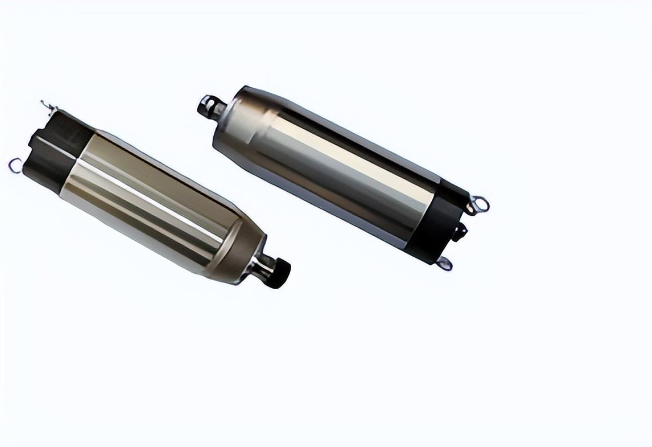
一、主轴在车床系统中的定位:驱动与支撑的双重使命
数控车床主轴的基本功能,是为工件提供稳定、高速的旋转运动,同时支撑加工过程中的切削力。它不仅是机械传动的一部分,更是实现高效精度加工的关键环节。其主要职责包括:
保持稳定的轴向与径向刚性;
提供可控的高速或低速旋转;
确保加工时的动态平衡;
在加工过程中吸收振动、减少共振现象。
简言之,主轴既要转得快,也要扛得住,还要稳得住。
二、核心性能参数:看懂主轴的“内在指标”
不同数控车床主轴虽外形相似,但其性能却千差万别。以下几项指标,是衡量其好坏的重要标准:
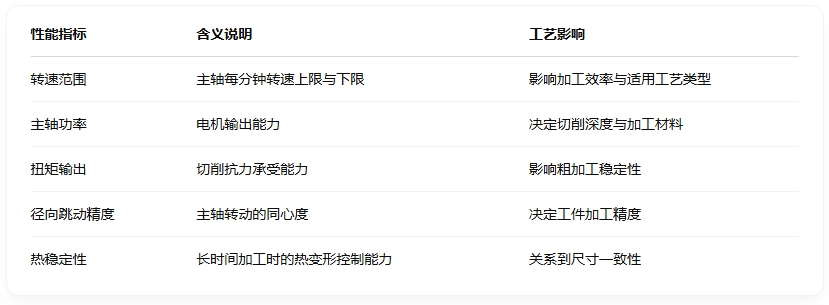
尤其是在精密加工或大批量生产中,这些参数往往决定了最终产品的合格率与一致性。
三、主轴结构类型对比:不同工况有不同的选项
数控车床的主轴大致可分为以下几种结构类型,每种类型对应的应用环境不同:
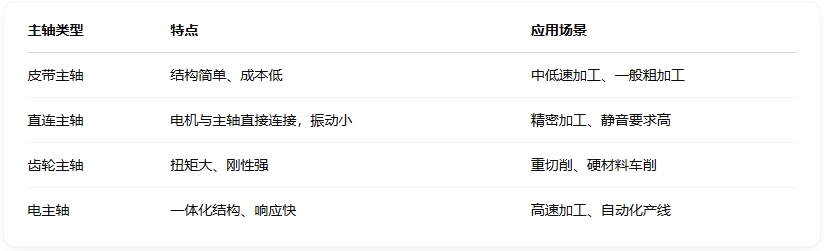
合理选择主轴类型,是提升加工质量、控制成本的重要环节。
四、加工工艺与主轴适配:不能“将就”的技术匹配
不同工艺对主轴的要求各不相同。选错主轴不仅影响效率,更可能造成设备过载或工件报废。
加工工艺主轴要求原因分析
精车高转速、低振动提高表面光洁度
粗车高扭矩、高刚性应对大切削量
螺纹加工精密定位能力强防止螺距误差
非金属切削控制转速与温升避免材料变形或烧焦
因此,在编制加工工艺路线时,主轴性能要与工艺参数形成精准对接,不能“只看转速不看扭矩”。
五、智能化趋势下的主轴技术升级
随着智能制造的发展,数控车床主轴也在向智能化方向不断演化,逐渐摆脱传统机械驱动的“单一角色”。
智能化发展趋势包括:
状态监测系统集成:实时监控振动、温升、噪音、润滑状态;
云端参数上传:主轴运行数据上传至MES系统,实现远程维护;
自动识别负载调整转速:根据切削力实时调整主轴响应;
磁浮悬浮技术尝试:减少摩擦与热量,延长寿命(实验阶段);
主轴“健康档案”建立:提前预警寿命临界点,防止突然停机。
这些进步将主轴从“被动执行单元”升级为“智能反应节点”。
六、主轴选型策略:从使用目的出发系统思考
面对市面上众多型号和品牌的数控车床主轴,选型要遵循几个原则:
加工目标清晰:是高精度加工、还是批量粗车?定位精准是前提。
考虑材料属性:硬质合金、合金钢、塑料等材料对主轴刚性要求不同。
设备系统配合:主轴类型需与车床床身刚性、刀塔配置、刀柄标准匹配。
维护与更换便利性:维修频率、配件成本也应纳入考虑。
预算与性价比平衡:避免过度配置,影响整体投入产出比。
主轴不是孤立存在的零件,而是车床系统中的一部分,不能单独看参数决定选型。
七、主轴管理与保养:决定使用年限的“幕后功臣”
即便是性能优异的主轴,如果保养不到位,也容易出现故障甚至报废。合理的管理机制有助于延长主轴寿命,保障生产连续性。
日常管理建议:
定期检查轴承间隙与主轴跳动;
主轴启动前进行低速预热运转;
使用正规润滑油,避免油质污染;
严格控制刀具装卸力度,避免锥孔损伤;
对主轴锥孔、内腔进行周期性除尘清理;
主轴加工完毕应空转降温,避免热应力积累。
良好的使用习惯,胜过频繁维修。
八、行业应用实况:主轴如何影响产业效率
在汽车制造、航空航天、轨道交通、精密模具等行业中,主轴的配置常成为产线效率提升的关键节点。
汽车发动机轴加工:对同心度、跳动极为敏感,主轴要求极高;
航空涡轮件车削:高速轻切削,主轴要有良好的动平衡能力;
重型设备零部件:需要耐高载荷的齿轮传动主轴;
医疗设备加工:超小型高精度电主轴逐渐替代传统配置。
不同行业的实践不断推动主轴技术的深化和多样化发展。
结语:主轴不是单一构件,而是效率背后的力量
数控车床主轴,作为“动力源”与“精度守门人”,不仅仅在机械层面起到作用,它更承载着从加工工艺、技术升级到智能制造的数据连接。理解主轴,就是理解整个加工系统如何运转的开始。
它不仅让刀具转起来,更让效率提上去,让品质稳下来。在快速发展的制造环境中,把握好主轴的每一个细节,才能在竞争中真正领先一步。